In six decades of work for the legendary Calcutt & Sons, Ian Compton has overseen some remarkable innovation in saddlery and riding attire
In 1959, I went to work with Joan Calcutt, who had started a second-hand tack business supplying the local riding fraternity. We worked tirelessly seven days a week, expanding the business, which included attending local shows and gymkhanas. At the time of Joan’s death in 1980, we had become one of the largest saddlers and riding outfitters in the country.
The following years were very innovative and productive, and I have been fortunate in employing very talented tradespeople as well as loyal staff, some of whom have been with me for more than 40 years.
Those of my generation will remember that only clipped horses had a jute night rug with an under-blanket, secured by a roller. With the help of a seamstress, we made a heavy canvas New Zealand rug with a gusset over the shoulder and no surcingle – which gave freedom of movement over the shoulder and didn’t slip. They lasted for years, unlike some of the enormous selection of synthetic materials now available.
All bridlework was in London tan and hand-stitched. The increasing popularity in showing and the riding clubs meant we designed our own working pony saddle and a straighter-cut flap on a general purpose (GP), which we called our “GD” (general dressage).
When Monty Roberts first visited England, we made his prototype quarter rug, which was his way of solving the problem of nervous racehorses entering the stalls, and we also supplied him with a quantity of sweet iron bits for his theory of making horses salivate.
A most unusual request came from Sheikh Mohammed, who summoned me to visit him in London. He produced a very heavy Argentine breaking saddle, similar in shape to an Australian stock saddle, and wanted a very lightweight version for endurance riding.
We had a carbon-fibre tree made which was covered with a full sheepskin seat and weighed 3.5kg. They were very successful and we received repeated orders.
We led the way with polo equipment in the 1970s. Alan Kent, the English eight-goal polo player, enquired if we could supply a patron with a set of tack, so with samples he lent us, we embarked on supplying the clubs with bridlework, specialist bits and the Calcutt’s polo saddle for many years.
From another chance meeting, we started making polo helmets. An orthopaedic company produced a thermoplastic shell and so we started making polo caps with a choice of team colours, followed by a faceguard. Production only recently ceased, with the changes to safety certifications.
In the 1960s, only cotton and cavalry twill was available for riding in, so a nylon stretch material was introduced and the rest is history.
Before Harry Hall was acquired by Austin Reed, the factory was 20 minutes away. I frequently stocked up on legwear, and before the factory closed we purchased a quantity of redundant stock including 60 pairs of ladies’ cotton breeches. These were put in the loft and forgotten about, and by chance were rediscovered recently; because they were “full cut”, they all sold within weeks.
Due to the popularity we purchased a heavy beige cotton and are now producing men’s and ladies’ breeches in beige.
Although business has changed dramatically with the advent of the internet, our specialities have become more traditional, not less. We have acquired a hunt button engraver after our engraver retired, and I have resurrected the Henry Keats business making hunting horns.
The saddlery businesses that do survive will become more essential in providing a service in repairs and bespoke bridlework and hunting attire. With the support of the riding public, I hope our old traditions will survive.
● As told to Aurora Eastwood
You can also read this feature in the 27 May issue of Horse & Hound magazine.
You might also be interested in…
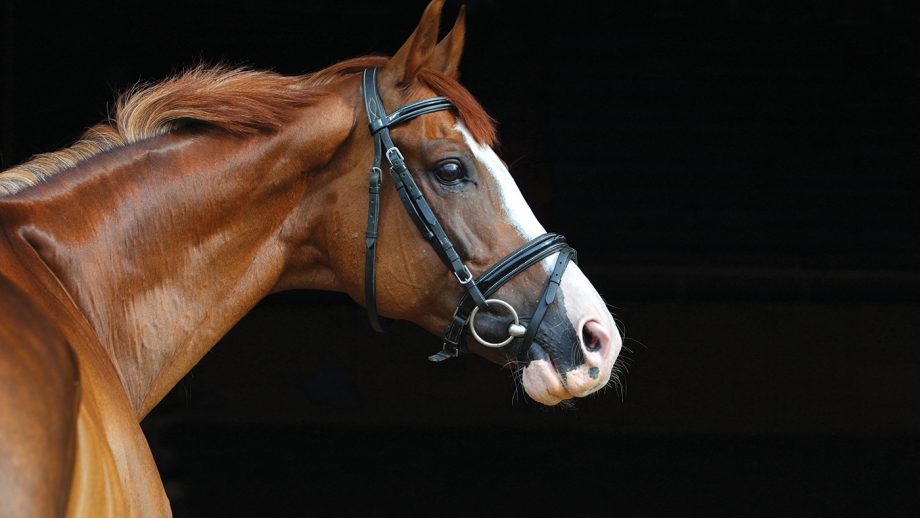
How bridle pressure affects a horse’s performance *H&H Plus*
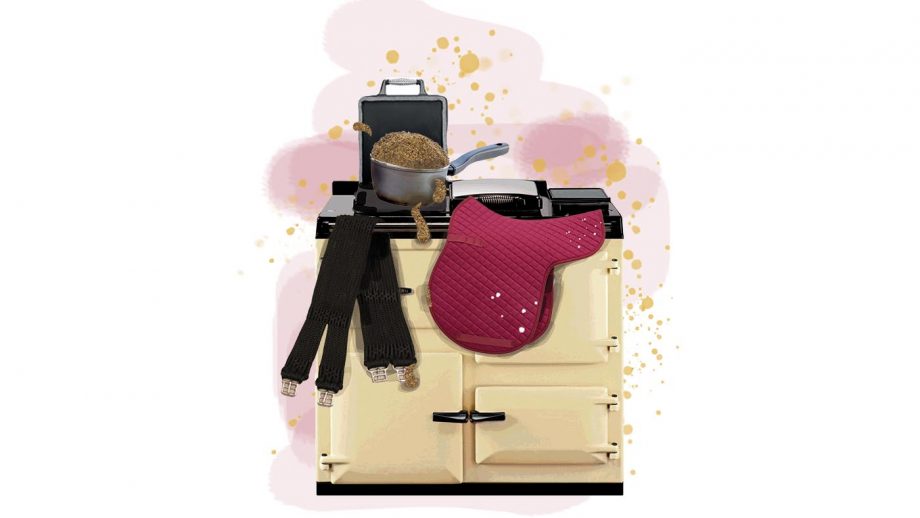
Ye olde tackroom: horsey items to take you on a trip down memory lane *H&H Plus*
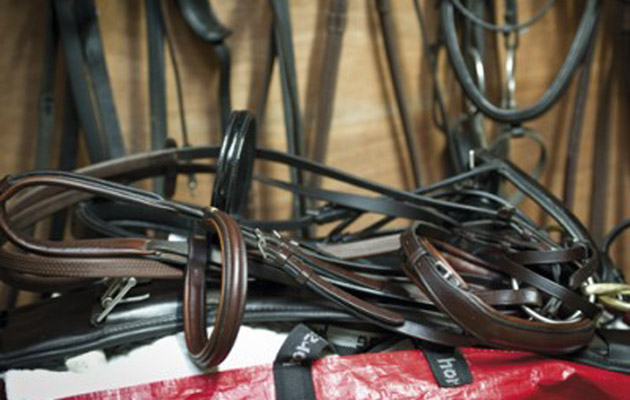
11 warning signs your tack room is out of control
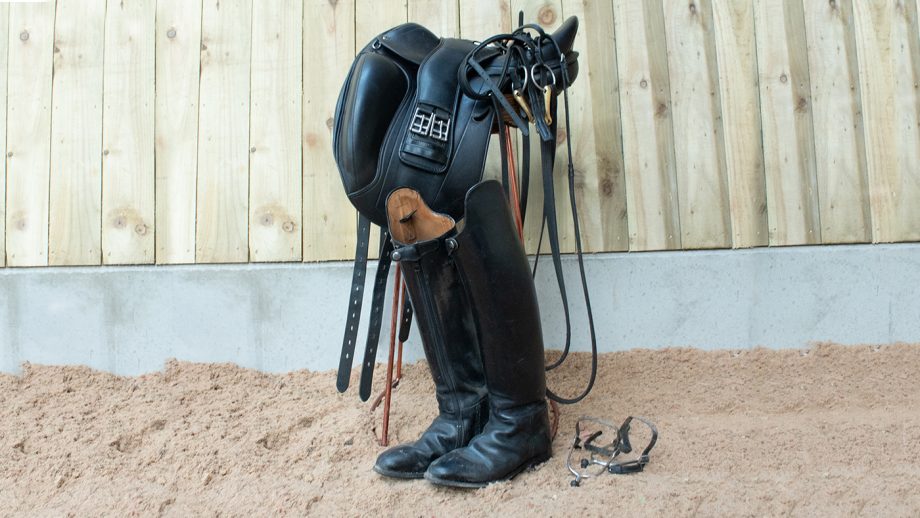
Fed up of cleaning muddy tack? Check out H&H’s most efficient ways to care for your leather tack
H&H offers advice on how best to care for your leather equipment to make sure it stands the test of